I had gotten to a point where I've been wanting to post the update of rebuilding and re-accumulating parts and accessories for an all American lathe set up (as might of been used by early American watch makers), and then well life happened and I got busy with other stuff. Well, I thought before waiting any more I would update this thread as William was interested in seeing the set up when it was completed. Well, it's not completed yet, but I have collected many parts and made a few to complete unfinished and broken ones like the handle on the turn for the mill, a custom wood base, a foot for a older era Marshall cross slide, and even made my own spring operated pinning set up for catching the index out of a cheap case back opening tool, and was able to find a way of attaching an index to the headstock collet holder (of course it is crude and needs re-thinking). Did a lot of refinishing and replacing of old rusted out and oxidized accessories. What's left is a proper rigging of the countershafts, pulley set up, and gear cutters, etc. Any added thoughts?
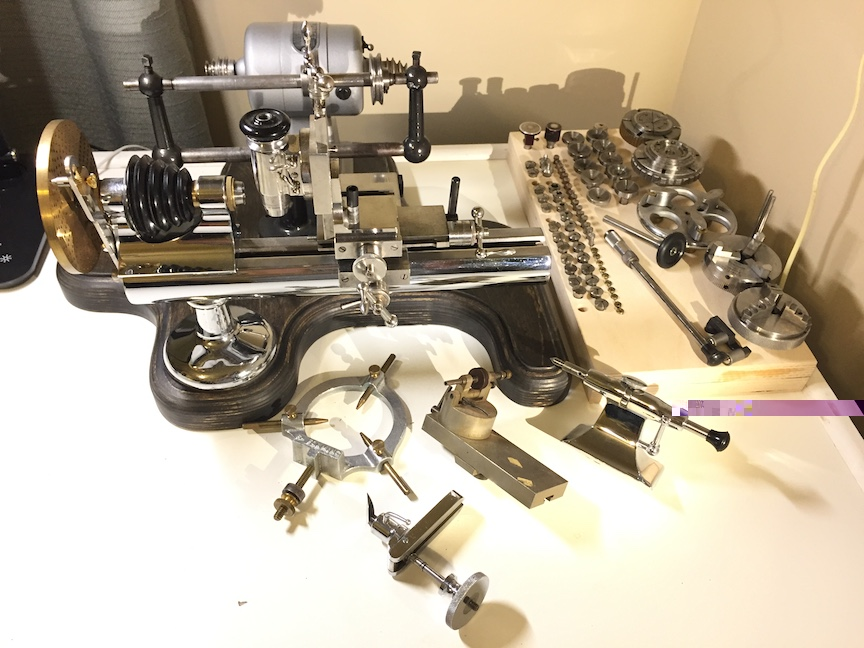
- IMG_2239.JPG (185.07 KiB) Viewed 11218 times
Some of the brands used are Peerless, Marshall, Hardinge, Snyder, Early Levin, Witcomb, Fleming, etc. However there is one modern Sherline chuck in the mix, and a Borel six jaw chuck.
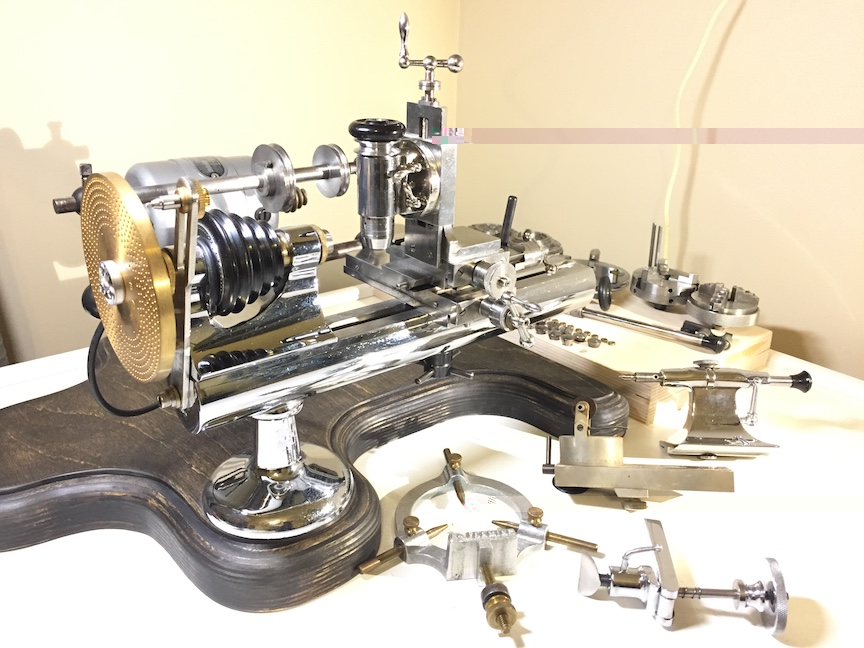
- IMG_2232.JPG (186.93 KiB) Viewed 11218 times

- IMG_2236.JPG (310.79 KiB) Viewed 11218 times
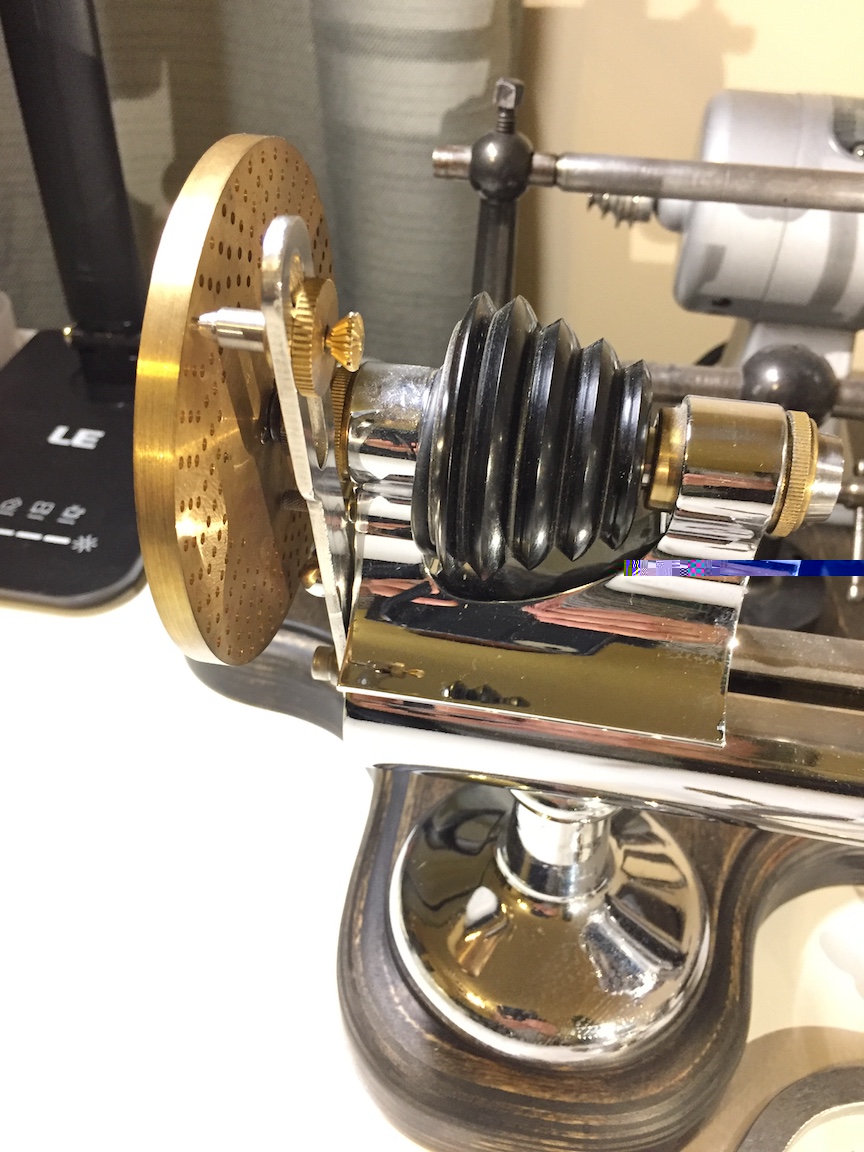
- IMG_2234.JPG (293.08 KiB) Viewed 11218 times